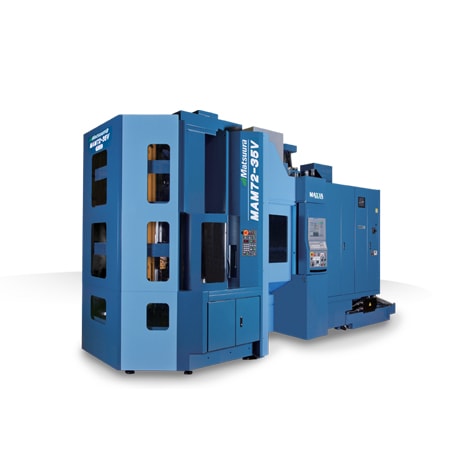
St. Paul, MN — (June 24, 2019) From Canadian Metalworking Magazine, Joe Thompson:
The simultaneous machining work of multitasking centers typically includes the turning and multisided milling of complex parts with tight tolerances. Secondary spindles and large-capacity ATCs give this type of machine tool the ability to completely finish a part in one setup.
The addition of automation enables this work to continue unattended, freeing up operators to work on several machines at once, rather than having them spend all their time on load/unload tasks at a single machine.
Automation traditionally has been viewed as a requirement for high-volume production runs of one particular part. However, the manufacturing industry is changing, and the high-mix production common in multitasking now is becoming the norm.
Manufacturing technology has been forced to keep pace with these changes. But automation comes in many forms, and while complex robotic installations have their place, simpler options also are available.
“Automating a machine doesn’t necessarily mean putting a robot in front of it,” explained Kevin Smith, turning products manager for Elliott Matsuura Canada. “The word automation gets everybody excited, but they also can get scared about it. It doesn’t necessarily have to be such a complicated process. Shops can get introduced to automation on the simplest scale, like a bar feeder or parts catcher, and go from there.”
Simple, in-situ automation includes conveyors and parts catchers integrated into a machine tool by the builder or distributor. It’s often beneficial for shops to understand that these common, well-understood accessories are, in fact, a type of automation and can lead to further, more complex automation being installed in the future.
“Once shops see the power of simple automation that’s already built into the machine, it’s easier for them to accept automation that is a little more complicated. Pretty soon they are asking about collaborative robots and completely automated workcells,” said Smith.
Load/unload
In multitasking equipment, a pallet system, in both vertical and horizontal configurations, is a popular method of automating a process. With this type of setup, a pallet can be loaded with raw material outside of the machine while parts are being created in the work zone. Then, when the pallets are swapped, finished parts can be unloaded and the process starts again.
High-mix production
If a job requires unattended machining of a high mix of parts, the problem area always has been changeovers, which typically need to be done manually. But now technology exists that removes this roadblock by using a robot to change the chuck jaws.
As part of a machining cell, this setup enables the operator to prepare the machine to run different parts in low volumes.
This new type of automation practice is more flexible than in years past when dedicated systems were good for only one part. When that part was no longer being produced, automation systems – particularly robots – were mothballed, often never to be used again.
“The phrase today’s automation is a good one, because we are not talking about the same automation from even five years ago. It’s become simpler and more flexible, and it’s not cost-prohibitive anymore either,” said Smith. “In yesterday’s automation it also was necessary to bring in an automation specialist. What you essentially need now is somebody who knows how to use an iPhone®. It’s really that simple.”
If an operator is no longer standing in front of one machine for an entire shift, the machine is going to run continuously for the full shift (or two or more shifts) without being stopped to complete a new setup. Skilled workers no longer need to simply load the chuck and press cycle start. They can now leave the machine and go over to another machine.
“I don’t believe that robots are going to eliminate the need for workers either,” said Smith. “They are going to eliminate the need for some of the unskilled work, and those workers can be upskilled and put on new tasks.”
Automation and tooling
One of these tasks that can be shifted to a now freed-up operator is tool assembly, a job that cannot be handed off to a robot.
“Mill/turn machines need more tools than stand-alone machine because they are engaging in multiple types of machining work. In an automated setup, the machine will run for a longer period, and therefore more tooling, especially redundant tooling, will be required,” said Fischer. “If you will be running long periods of unattended operation, a large-capacity toolchanger is required.”
It’s a good idea to load the ATC with the tools that are used the most and those that wear the fastest.
To read this article in its entirety, please click HERE.
To learn more about Elliott Matsuura Canada, please visit: https://www.elliottmachinery.com/
Joe Thompson can be reached at: [email protected].
Matsuura Machinery USA, Inc., located in St. Paul, MN is the U.S. subsidiary of Matsuura Machinery Corporation in Japan. Since 1935, Matsuura has been the forerunner in designing innovative technology and manufacturing solutions to a variety of industries around the globe. Matsuura Machinery USA, Inc. delivers unmatched excellence in 5-axis, vertical, horizontal, linear motor, multi-tasking CNC machine tools and machines with a powder bed metal AM platform with machining capability. Matsuura Machinery USA, Inc. provides the service, applications and technical field support that have always been the Matsuura standard for business. For more information on Matsuura products, contact: [email protected].